TIRE & RUBBER
We design world-class tire production solutions that set the standard for safety, productivity, quality and efficiency—empowering the industry’s top manufacturers with cutting-edge innovation and unmatched expertise.
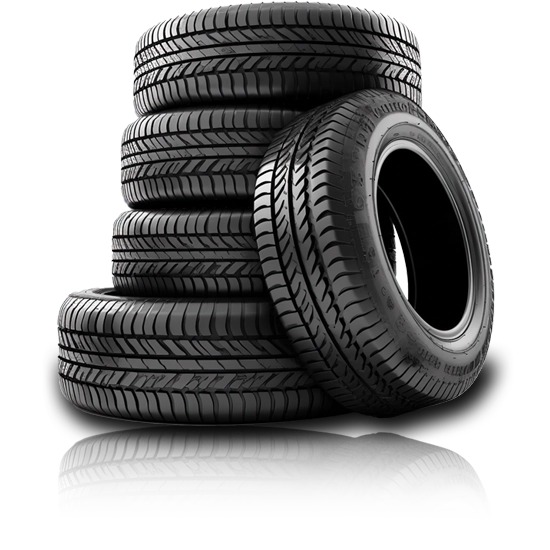
TIRE & RUBBER
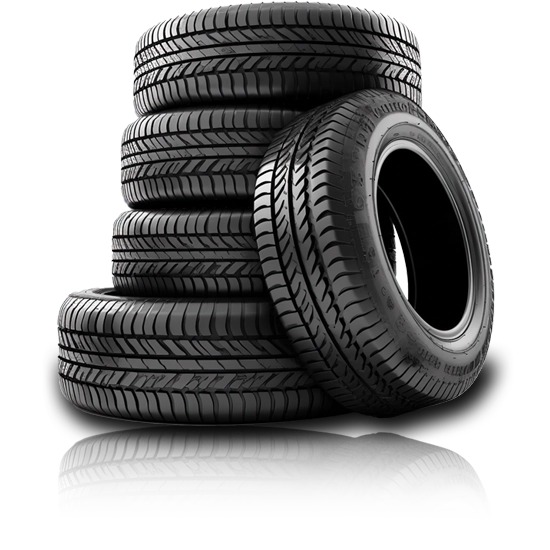
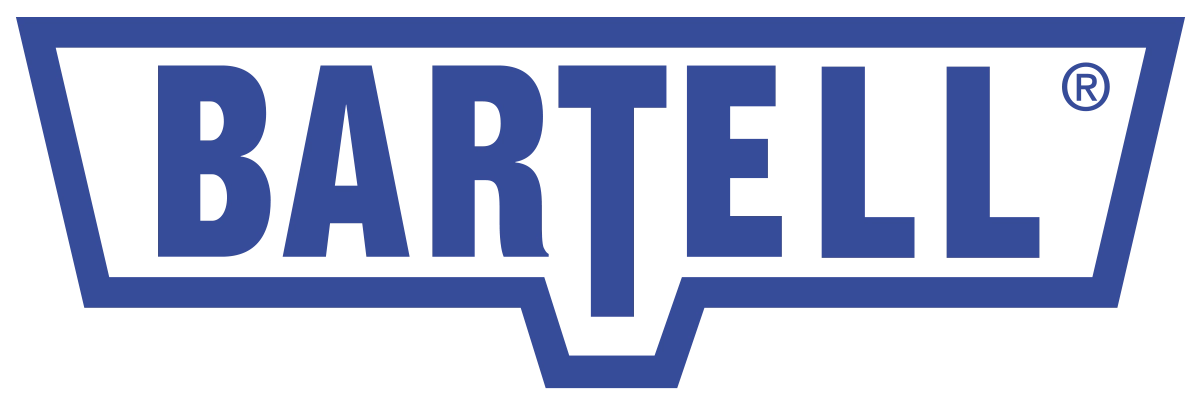
Products
As the global leader in tire bead winding solutions and testing equipment, Bartell empowers the world’s top tire manufacturers to maximize productivity, manufacturing efficiency, and end product quality.
Driven by relentless research, innovation, and deep process expertise, we develop technologies that set the benchmark for automation and reliability in tire bead production. With the largest global installation base of tire bead winding solutions, Bartell continues to lead the way, delivering quality and innovation which continue to redefine tire manufacturing.
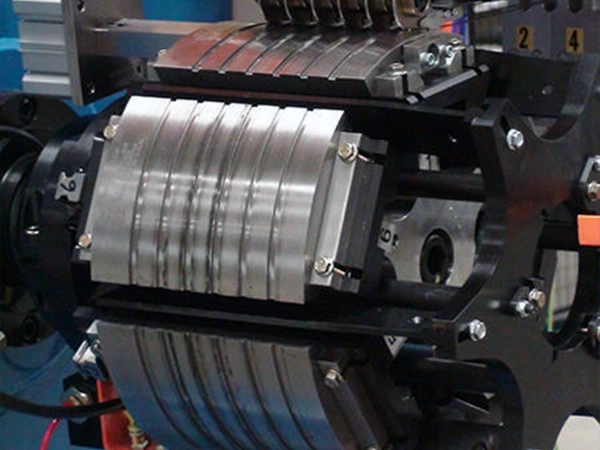
Bartell Bead Winding systems provide the worlds most efficient production systems with the highest quality available. With production systems capable of producing taper base, single wire hexagonal, square section, or weftless bead our configurations are designed to meet almost any application.
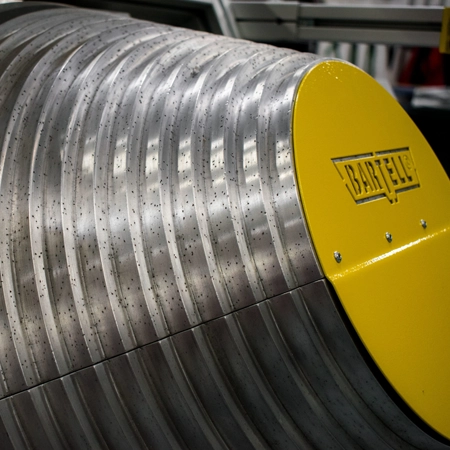
From mechanical measurement to advanced non-contact imaging our technologies provide the most accurate measurements available and include capabilities such as networking and data storage to provide easy statistical quality analysis and documentation.
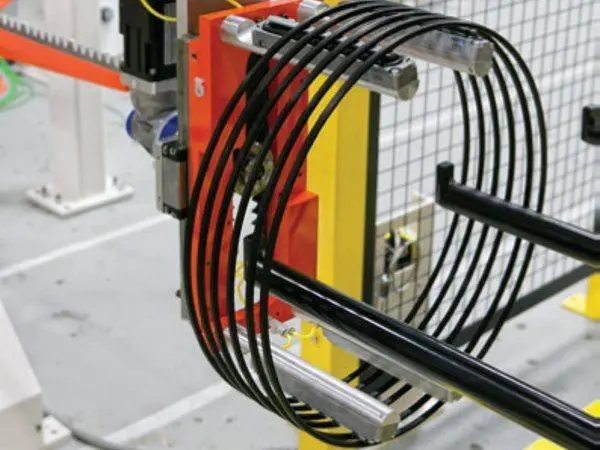
To improve the operational efficiency of the bead production process Bartell has listened to the market and developed innovative handling and transfer systems that can be directly integrated into new and existing Bartell Bead winding systems.
Industries
Our equipment for the passenger segment is capable of meeting all of your capacity demands. Taking into account the need for PCR at a high capacity, a single Bartell machine is capable of producing tire beads with square or hex profiles with a production capacity of 500,000 to 6.5 million beads per year.
When it comes to Trucks our integrated systems can give you a competitive advantage. Integrating bead winding and apexing allowing for greater efficiency for TBR, Taper Based Beads, and Splice Wrapping.
Financing Available!
See all the ways we can help your business grow for generations to come. Visit our Financing section to see all of our latest programs.